Metallographic Microscope Solutions
Metallographic microscopes (also known as metallurgical microscopes) are highly relevant across the value chain of various industries where metals are used, i.e., from mining via smelting to alloy development, recycling, and additive manufacturing. Metallographic microscopes can be used for research and development (R&D), quality assurance (QA), failure analysis (FA), or inspection.
Metallography is the study of the microstructure of all types of metals and metallic alloys. More concretely, observing and determining the structure, composition, and spatial distribution of grains, inclusions, and phases in these metals and metallic alloys.
Please contact us if you would like to have personal expert advice on our microscopy solutions for metallography.
What kind of samples do you observe?
If you observe sections, an upright metallographic microscope serves you well. If your samples are bulky and might not fit between the objective and the stage, you could use an inverted metallographic microscope.
Which standards do you need to follow for documentation?
Whichever standards you may need to follow, the dedicated Leica software modules allow you to perform analysis according to common international, regional, and organizational standards.
How complex are your tasks and samples?
If you only observe samples, without the need to document or measure, a manual microscope, such as the DM2700 M or the inverted DMi8 M, can serve you well. If you have more complex tasks at hand, a partially automated version, such as the DM4 M or the inverted DMi8 C, meets your workflow needs better. If you need to analyze many samples, the DM6 M or the inverted DMi8 A, is the better choice as the automated solution will help save you time.
Get your individual solution based on 3 short questions.
Dedicated configurations are available for your specific needs. Answer the short questionnaire to find the right solution for your needs. If you would rather have a representative contact you, then please click here to fill out your contact information.
Contact us{{ question.questionText }}
Please select an answer!
Best Match
{{ resultProduct.header }}
{{ resultProduct.subheader }}
{{ resultProduct.description }}
{{ resultProduct.features }}
Request Your Information Package
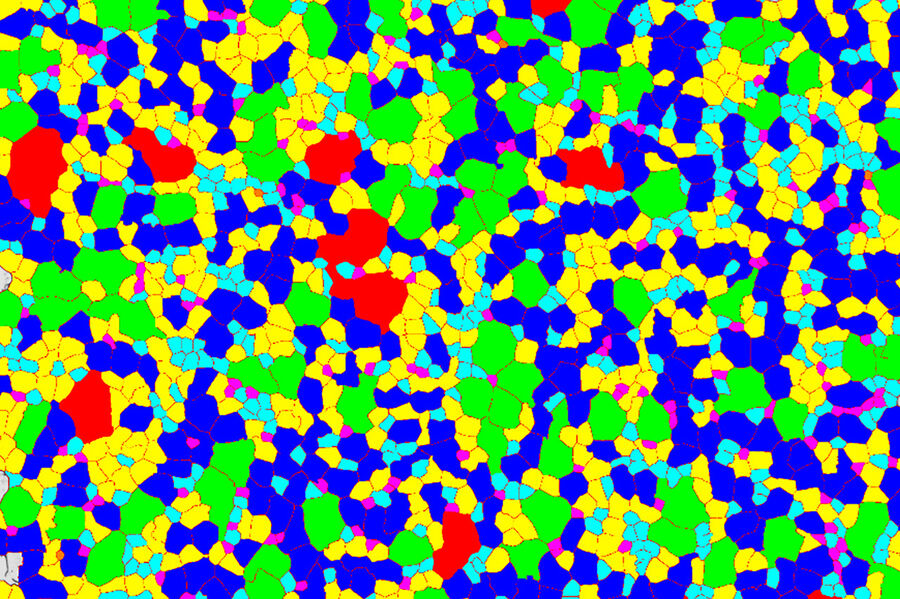
Insights for quantitative analysis
Leica metallographic microscopes help you gain insights into metals or alloys of interest. Such insights help you determine key parameters, like hardness or ductility, which influence how metals and alloys can be processed and their performance during machining.
Quantification as a means of understanding the material’s microstructure is key for these tasks, whether it be measuring grain size or determining the number of inclusions or phases in the metal or alloy sample.
Thus, cameras and software play an essential role for image acquisition, measurement, annotation, storing of data for documentation, and sharing of results.
Challenges in metallographic microscopy
Before a metallographic sample can be accurately and reliably analyzed, proper preparation is crucial. Usually, a section is cut, polished, and the microstructure of the sample made visible by etching.
To analyze the microstructure accurately, at times the minutest of details need to be observed, but this can be challenging with metallic samples that have highly reflective surfaces.
A variety of illumination and contrast methods can make all the difference when visualizing important details.
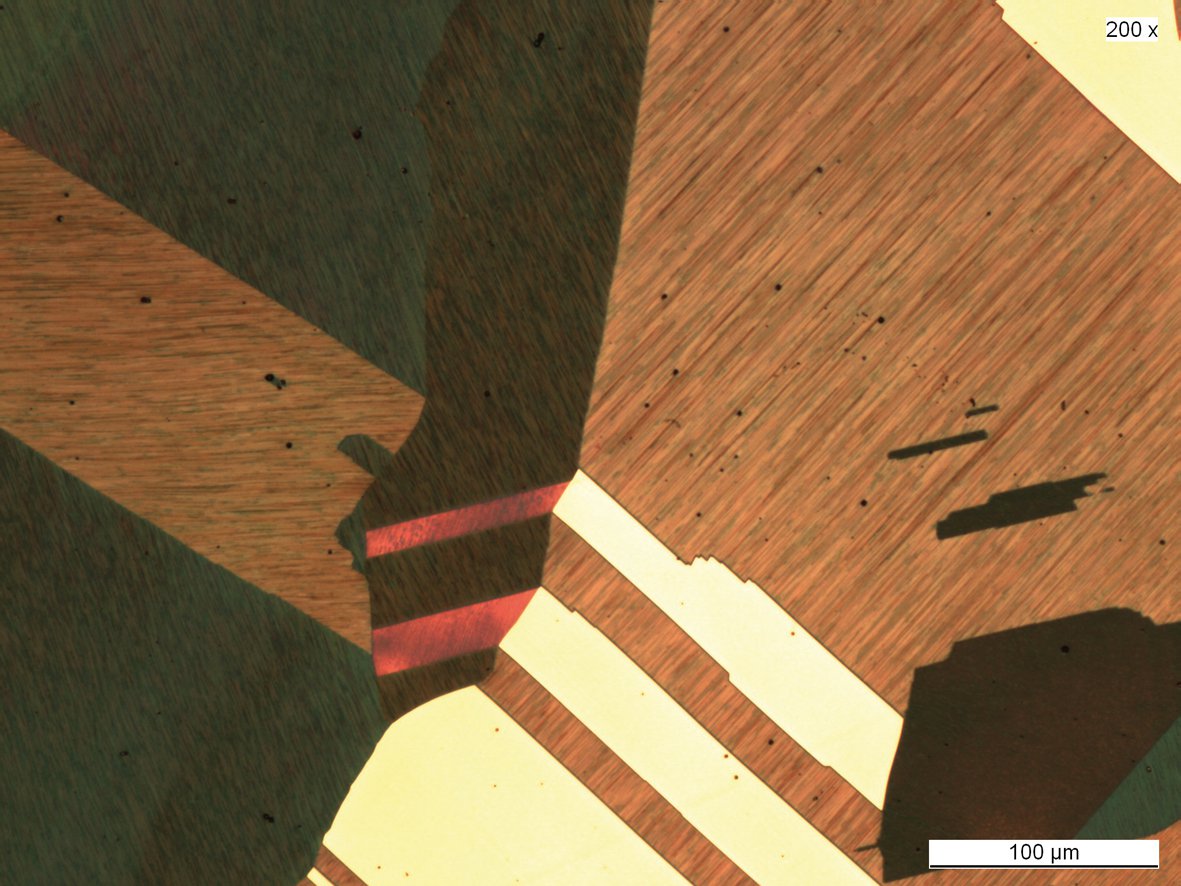
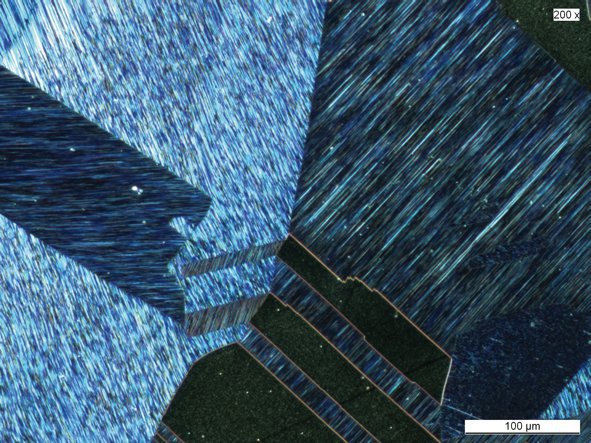
Example of a copper alloy sample imaged with brightfield (left) and darkfield (right) illumination.
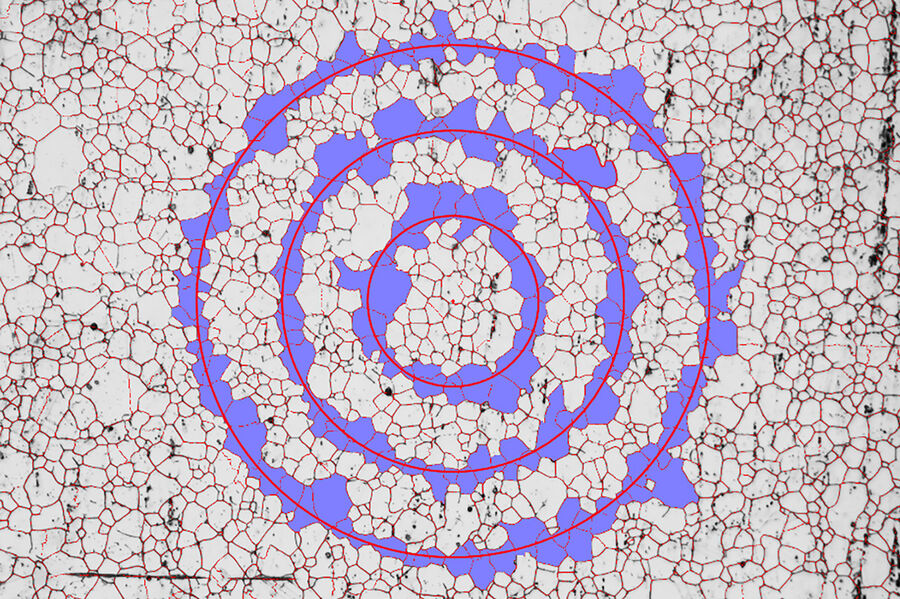
Grain size analysis
One important characteristic that influences the metal or alloy quality is grain size. Analyzing the grain size enables users to gather information about the tensile and yield strength, elongation at fracture, and the ductile-brittle transition temperature of metals and alloys. These characteristics heavily influence the performance.
Especially for complex alloys or materials, microscopes with the capability of automatically switching between several contrast methods can greatly help increase the efficiency of grain-size and -density analysis.
LAS X Grain Expert is a module dedicated to the structural analysis of steel and other materials.
Phase analysis
Phase analysis enables users to determine the number and nature of phases in the microstructure of metals and alloys.
Application examples include particle-density analysis of dispersed solids in alloys or the ratio of extractable ores in minerals. In the automotive industry, porous surfaces of catalysts and the honeycomb structure in light-weight construction materials could be performed with phase analysis.
Similar to grain analysis, the more complex the material analyzed, the more convenient it is to use a microscope with a partially or fully automated way to change illumination or contrast methods.
The software module LAS X Phase Expert is for the analysis of multiple phases and microstructure components.
Steel quality / inclusions
To assess the quality of steel, non-metallic inclusions need to be rated. This analysis is normally done according to international, regional, and organizational standards, whether the automotive and transportation, metalworking, or construction industry.
The LAS X Steel Expert software helps you to accurately and quickly rate non-metallic inclusions to ensure steel quality.
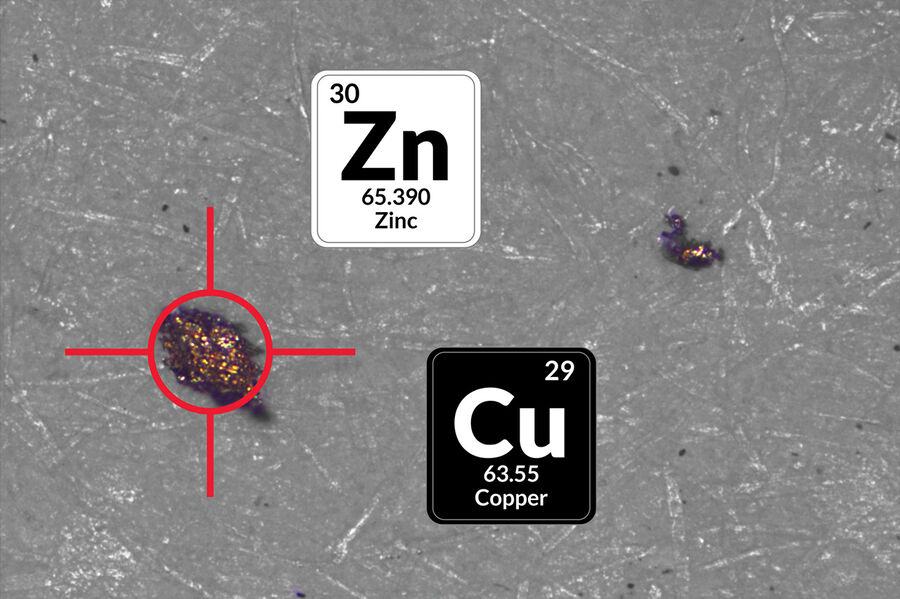

Cast iron
To determine the quality of cast iron, it is necessary to analyze the graphite microstructure. A wealth of information can be obtained about the shape, size, and distribution of graphite in nodular/ductile and vermicular/compacted cast irons.
The LAS X Cast Iron Expert software is dedicated to graphite and ferrite/pearlite analysis.
Decarburization
If steel is heat treated in air, the effect of this treatment is a measurable carbon depletion in exposed areas.
The LAS X Decarburization Expert software enables users to determine the quality of the heat-treated steel by analyzing the functional decarburization, i.e., the depth at which the original material properties have not been substantially affected.
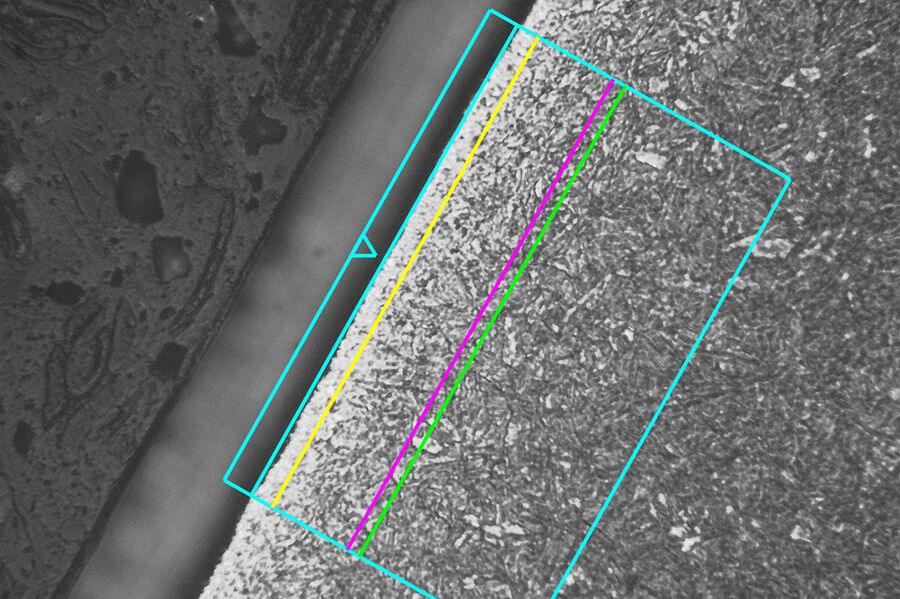
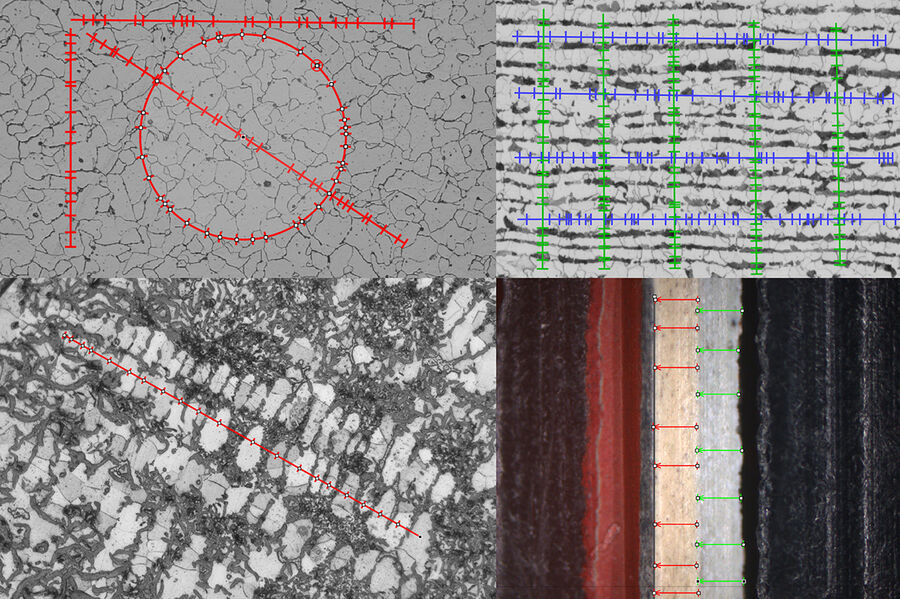
Metallography toolbox
Measurements are key for the stereological analysis of metallographic or metallurgical samples. This usually involves laborious manual tasks – and the danger of inaccuracies.
The LAS X Metallography Toolbox, an add-on to the LAS X 2D measurements software, simplifies manual tasks used when deriving calibration parameters from measurements, such as baseline lengths, lineal intercepts, point counting, segments of circles, or multi-layer coating thickness.
Both assigning individual classes to measurements as well as comparative analysis of the related parameters are possible. Thus, component or phase specific results can be generated.
Frequently Asked Questions Metallographic Microscope Solutions
Metallography is the study of the microstructure of all types of metals and metallic alloys. More precisely, it is the scientific observation and determination of the composition, crystalline structure, and spatial distribution of grains, inclusions, and phases. Many important macroscopic properties of metals are greatly influenced by the microstructure, e.g., tensile strength, elongation, and thermal or electrical properties. Understanding the relationship between microstructure and macroscopic properties is critical for the development, manufacture, and application of metallic alloys.
Metallurgy involves the study of the physical and chemical properties of metals and metallic alloys. It mainly concerns the design, development, and production of metals and alloys used in consumer products. The knowledge gained from metallography about metallic microstructure is very useful for metallurgy.
Metallurgy is the characterization, design, development, and production of metals and metallic alloys, while metallography is limited to the study of metallic microstructure.
A metallographic microscope (also known as a metallurgical microscope) takes advantage of different optical microscope techniques to reveal the microstructure of metals and alloys.
Examples include incident brightfield illumination as wells as less common contrast methods, like darkfield, differential interference contrast (DIC), and color (tint) etching.