Introduction
Products and applications in the industries of metal alloy, automotive, aerospace, transportation, and electronics, as well as in the fields of metallography, earth science, and materials science, require materials analysis [1-3]. Maintaining a cost-effective way to ensure product quality or reliable research results for innovation has becomes a serious concern in the face of increasing competition and ever-stricter standards.
Much time and money is spent using multiple techniques to visually inspect a material and then identify its local composition [1-3]. Visual inspection is done with high resolution and high contrast microscopy and composition is determined with chemical/elemental spectroscopic analysis. For specific applications, often it is crucial to have reliable data for a material’s microstructure and composition in order to determine a further course of action. This fact is especially true when serious time and budget limitations force the need to have a way to make quickly the right decision with confidence.
For some cases of inspection, quality control (QC), and failure analysis (FA), identifying multiple layers of coatings and composition variation from the base material to the surface are necessary [4-6]. Examples are found in the electronics (soldering and PCB surface coatings) and automotive/transport and construction (paint and anti-corrosion coatings) industries, as well as the field of forensics (accident investigation). Materials are often coated to give components or parts specific mechanical or electrical properties or simply to protect them against wear, weathering, and corrosion. The coatings can have multiple layers and consist of various materials. For inspection of components or parts with multi-layer coatings or composition variation from the bulk to the surface, depth profiling enables the composition of each layer or at different material depths to be determined. Furthermore, even the presence or absence of a critical layer can be shown.
The use of the DM6 M LIBS materials analysis solution from Leica Microsystems for depth profiling and layer analysis is described below.
Depth profile analysis of materials
The LIBS method exploits laser ablation to microdrill (µ-drill) into coatings and the component material. The ability to µ-drill allows the following:
- Depth profiling to determine composition change with depth into the material bulk;
- Layer analysis of painted or coated materials with multiple layers; and
- Surface cleaning to remove oxides or contamination.
Figure 1 shows an example of µ-drilling holes into a steel alloy.
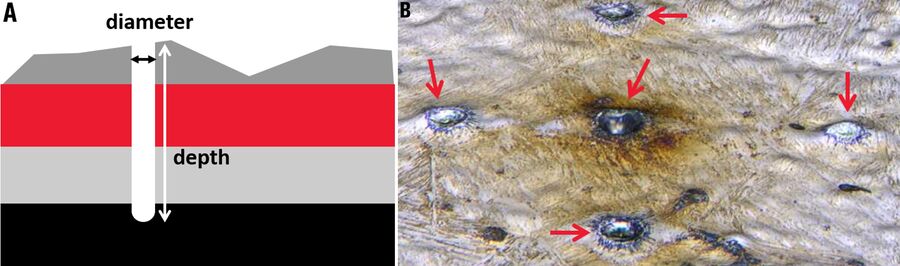
Layer analysis of a coated material
Depth profiling analysis was performed on a garter spring made of copper (Cu) and coated with nickel (Ni) and silver (Ag). The analysis was done using µ-drilling and LIBS with the DM6 M LIBS solution. Each layer and the bulk of the spring were analyzed.
Garter springs are coiled springs connected at each end which results in a circular shape. They are used for motor seals, belt-driven motors, and electrical connectors. A photo of the garter spring and schematic of the material cross section are shown in figure 2.
The data from the depth profiling analysis of the garter spring are shown below. Microdrilling with up to 8 laser shots was done on the spring material to analyze from the top layer to the bulk. Depending on the material, approximately 5 µm can be ablated at the focus position by each laser shot. The entire time needed to make the 8 laser shots and acquire the data for the 3 spectra was between 1 and 2 minutes.
The results in figure 2 show that the spectrum of the:
- Top layer was obtained with the 1st laser shot and it is composed of Ag;
- Next underlying layer was obtained with the 4th laser shot and it is composed of Ni; and
- Bulk was obtained with the 8th shot and it is composed of Cu.
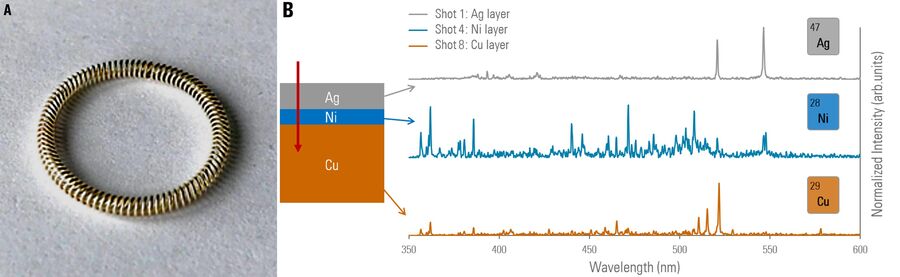
To determine how well the LIBS spectra data from each layer and the bulk material of the spring match with reference elemental spectra in the database, a quality of match value is calculated. The values are shown for each layer and the bulk in table 1 below. The element reference spectra with the highest quality of match to the measured spectra are then chosen to determine the material composition.
Layer | Spectrum from Laser Shot | Element Reference Name | Quality of Match |
Top | 1 | Silver (Ag) | 947 |
Underlying Top | 4 | Nickel (Ni) | 751 |
Bulk | 8 | Copper (Cu) | 866 |
Table 1: Quality of match values for the garter spring spectra obtained with LIBS when compared to reference spectra from the database for the specific elements Ag, Ni, and Cu.
Summary
In this report, the use of the DM6 M LIBS materials analysis solution from Leica Microsystems for efficient depth profiling analysis of a coated garter spring (motor or electronic components) has been described. Microdrilling into the material and obtaining spectra for the 2 coat layers and the bulk material of the spring took 1 to 2 minutes.
Materials analysis is important for many types of product development (R&D), quality control (QC), failure analysis (FA), and technical applications and is used routinely in multiple industries and fields. Often the time and expense allocated for materials analysis is limited, but obtaining reliable results and achieving product quality always remains a priority [1-3].
For inspection, QC, or FA of components with multiple layers of coatings or a composition variation within the material, sometimes it is necessary to do depth profiling. Paint and anti-corrosion coatings are examples. Depth profiling enables composition determination of each layer and at different depths within a material.
Further reading
- J. DeRose, K. Scheffler, See the Structure with Microscopy - Know the Composition with Laser Spectroscopy: Rapid, Complete Materials Analysis with a 2-Methods-In-1 Solution (2018) Science Lab, Leica Microsystems.
- J. DeRose, K. Scheffler, K. Kartaschew, M. Horz, T. Locherer, Visual and Chemical Analysis of Steel Microstructure: Faster Rating of Steel Quality: A 2-Methods-In-1 Solution Combining Microscopy and Laser Spectroscopy (2020) Science Lab, Leica Microsystems.
- J. DeRose, K. Scheffler, Cleanliness Analysis with a 2-methods-in-1 solution: See the particles and know their composition at the same time (2019) Science Lab, Leica Microsystems.
- H. Kondo, M. Aimoto, H. Yamamura, T. Toh, Rapid Inspection of Defects of Steel by Laser Induced Breakdown Spectroscopy, Nippon Steel technical report no. 100 (2011).
- T. Kim, C-T. Lin, Laser-Induced Breakdown Spectroscopy, Chapter 5 in Advanced Aspects of Spectroscopy, M.A. Farrukh, Editor, IntechOpen (2012) DOI: 10.5772/48281.
- C. Meinhardt, V. Sturm, R. Fleige, C. Fricke-Begemann, R. Noll, Laser-induced breakdown spectroscopy of scaled steel samples taken from continuous casting blooms, Spectrochimica Acta Part B, vol. 123 (2016) pp. 171–178, DOI: 10.1016/j.sab.2016.08.013.