Grain size and alloy properties
It has been well known for a long time that as the grain size increases, the alloy’s (refer to figure 1) [1]:
- tensile strength (Rm) and yield strength (Re) decrease;
- elongation at fracture (A%) increases; and
- ductile-brittle transition temperature increases.
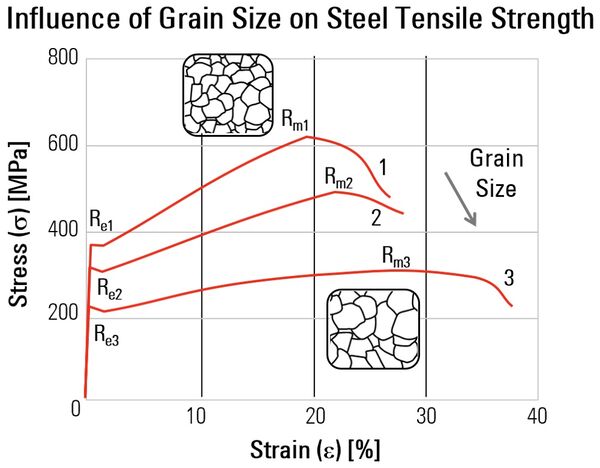
Microstructure analysis: alloy sample preparation workflow
In order to characterize the microstructure of an alloy, a sample has to be prepared from the alloy material, then ground and polished, imaged with a microscope, and finally the images are analyzed. Figure 2 shows a diagram illustrating the typical workflow for sample preparation and microstructural analysis.
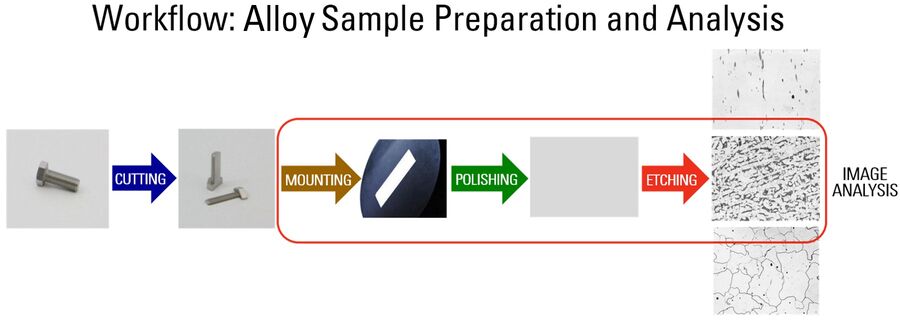
Techniques for microstructure analysis
Different types of experimental techniques are used to investigate the microstructure of alloys. For more than 100 years, optical microscopy, using incident brightfield, darkfield, differential interference contrast (DIC), and polarized light illumination along with color etching, has been the most common method. At the present time, computer automated microscopes and image analysis systems provide a rapid and accurate way to evaluate such alloys.
The setup and analytical capabilities of the imaging software used has a very important effect on the accuracy, reliability, reproducibility, and efficiency of:
- image capture and analysis;
- grain size and microstructure evaluation; and
- report generation from the results.
LAS/LAS X Grain Expert software
A Leica microscope using the