Webinar
Watch the webinar: Practical Applications of Broad Ion Beam Milling
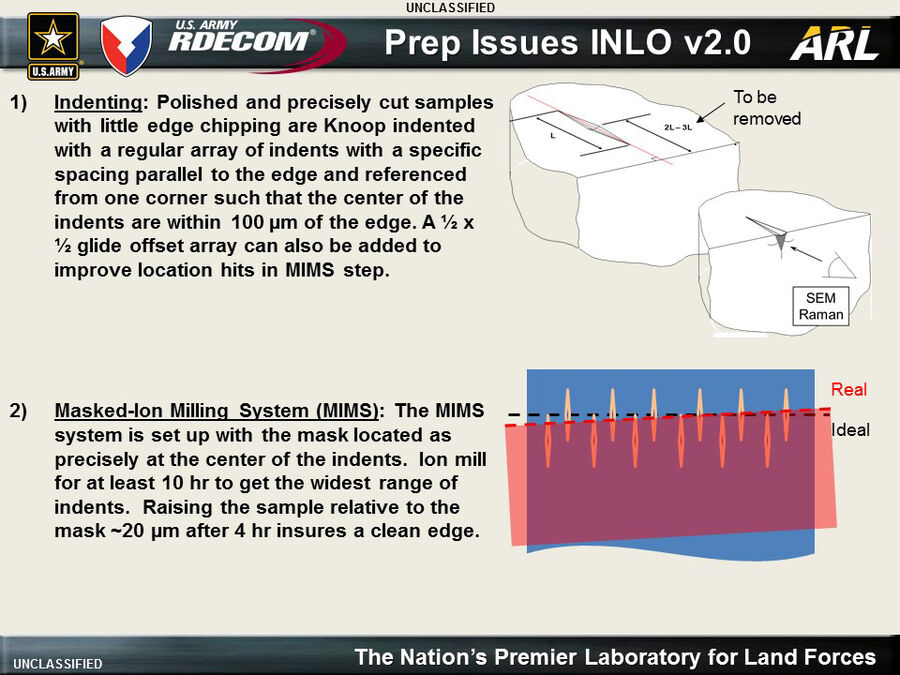
Interview
WALCK: I'm a contract Senior Scientist working at the Aberdeen Proving Ground for SURVICE Engineering Company. We perform analysis on various materials using SEM, TEM and EBSD imaging applications. As such, we have numerous users at the lab currently using the EM TIC3X workflow. Due to the nature of the materials we use, our samples are more difficult to prepare than most.
For my work, I primarily use the EM TIC3X in a multi-step TEM sample preparation technique that we use to look at highly deformed ceramic materials that are used in armor ceramic applications. Our lab is also used for polymeric and light alloy analysis.
Ultimately, why did you choose the EM TIC3X ion beam miller for your lab?
WALCK: From previous work with ion beam milling, I knew that I could get very good results for EBSD with ion beam polishing, either with prior mechanical preparation or just through ion beam milling alone. The Army works a lot with powder processing for both metals and ceramics. Ion milling can preserve the microstructures of porous samples, whereas mechanical polishing can fill in and obscure the detail that you really need.
We have a lot of different materials being processed; polymerics, ceramics, metals. I knew we needed a cryogenic system, and the EM TIC3X gave us the best performance in terms of the amount of time we could keep the sample at temperature as well as the lowest temperature at the sample.
The mask alignment compared to some other systems also fit our needs better – with the EM TIC3X, you can maneuver the sample relative to the mask for cross sectioning in such a way that you do not touch the sample, which was important to us.
And, of course, automation was important. With the EM TIC3X, the user walks away during polishing of cross sections; automatic polishing means we don't have to manually perform mechanical polishing, as we would with tripod polishing for example.
Please discuss some sample preparation techniques for which you use the EM TIC3X.
WALCK: Sure. First, a colleague wanted to put together ultra-high molecular weight polyethylene laminate with a pressing process done at 100°C under 3000 PSI, and he wanted to look at the cross section. We tried mechanical polishing and ultramicrotoming, but the sample came apart. However, when we used the EM TIC3X at -100°C at 15 hours, we could see through 7 plys of the polyethylene. In the example, you can see the polyurethane binder at the interface between the UHMPE. This gave a very good method for evaluating these polymeric materials.
Colleagues in the metals division are looking at some light element alloys. The example here shows results from EBSD of magnesium. Mechanical polishing on this material doesn't work very well. Initially, they used mechanical polishing with a rotary stage with acceptable results. It wasn't until they used the standard stage with the cryo stage of the EM TIC3X that they got very good results. They had concerns that the ion beam might be heating some of the samples and re-crystallizing them (which was the case with some nickel alloys that were nanocrystalline). Ion milling at -50°C with the cryo stage of the EM TIC3X worked very well and provided great results. Ti6-4 alloy can also be very difficult to work with, and they were able to get very good results with that as well.
TEM imaging gives us an idea of the deformation mechanisms in the armor ceramics we're examining. The two materials we're using are Silicon Carbide (SiC) and Boron Carbide (B4C). We've developed some good techniques for sample preparation which we were able to publish.
We use a "macro" indentation procedure to simulate ballistic events with armor plates. Our main challenge is that under the indentation procedure, it's difficult to prepare a sample and preserve cracking and fragmentation without introducing artifacts. Previous sample preparation methods gave insights into a ballistic response, but no way to determine the origin of fragments. Prior nano-indentation work made for easy TEM sample prep, but was not an accurate predictor of ballistic response. We use a Knoop indentation, and as you increase the load you get more and more deformation. At the highest loads, you start to get spallation, which is why we could not touch the mask to the surface - with ion beam milling, there's a bit of welding that occurs, and if the mask touches the surface some material is lost.
Originally, our workflow used a tripod polisher to pre-thin the samples prior to impregnation. What we found was that we got cracking during multiple stages of the FIB process following polishing. We also found that when we performed the tripod polishing of the cross section, no matter how fine grit we used we'd always see deformation along the edges of the indent. We tried filling the indentation with a low-viscosity epoxy, but couldn't get good infiltration past the surface. Eventually, we developed a process of tripod polishing, then FIB (focused ion beam) polishing, then epoxy infiltration, followed by another FIB application to thin the sample. It was very time consuming and demanding; tripod polishing alone took about two days of manual processing. We had to come up with a faster, more automated method.
We replaced the tripod polisher with the EM TIC3X to make the initial cross sections, which gave us samples with exposed cracks that enabled us to move directly to vacuum infiltration and eliminate the FIB. We've also just purchased an EM TXP to improve some of our results by using the high speed diamond saw - we haven't used it yet, but are looking forward to great results. Using this new method, our prep time has dropped from more than two days to 10 hours, and we're able to get outstanding cross sections that lead to precise imaging for examination and indexing. We've been able to observe deformation mechanisms we never could before, such as nanoscale amorphous slip bands, slip band assisted microcracking, and both diffuse and abrupt elastic/inelastic boundaries.