Rate the Quality of Your Steel: Free Webinar and Report
Overview of standard analysis methods and practical solutions for evaluating steel inclusions
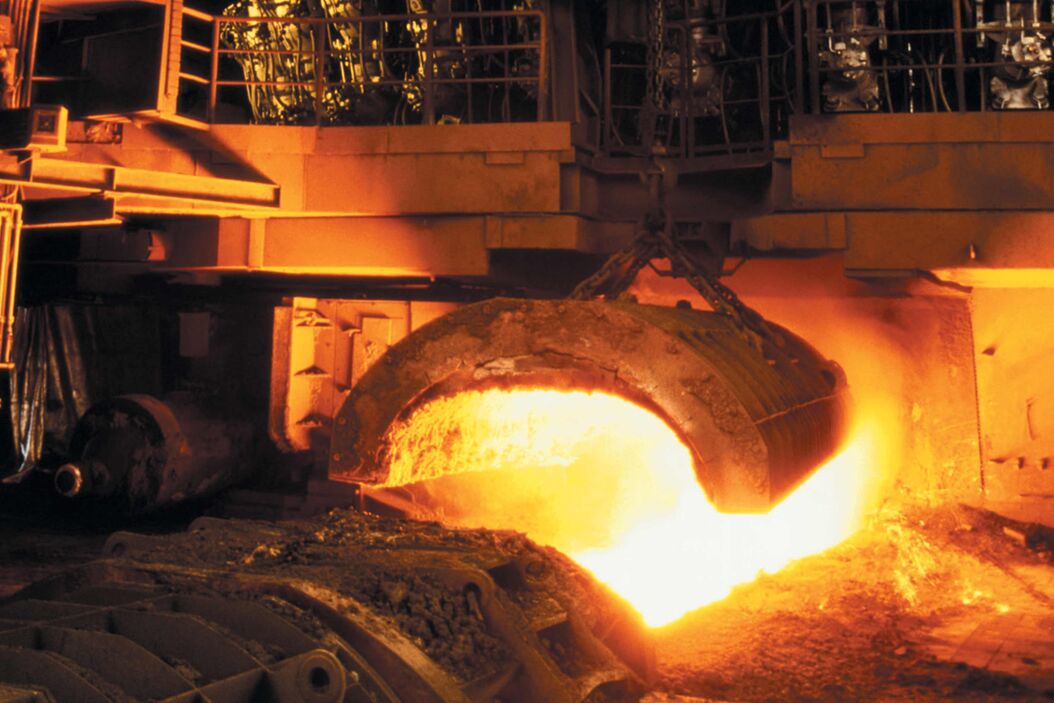
This webinar and report describe optimal microscopy solutions for rating steel quality in terms of non-metallic inclusions and review the various international and regional standards concerning rigorous quality assessment methods, e.g., EN 10247, ASTM E45, DIN 50602, and ISO 4967.
Superior steel quality is critical for a variety of industries and applications, especially for the manufacture of vehicles and ships and construction of buildings. Reliable and precise evaluation methods for non-metallic inclusions are key to determining their influence on the quality of steel. The combination of the